Material Handling Automation Solutions: A Must-read Guide
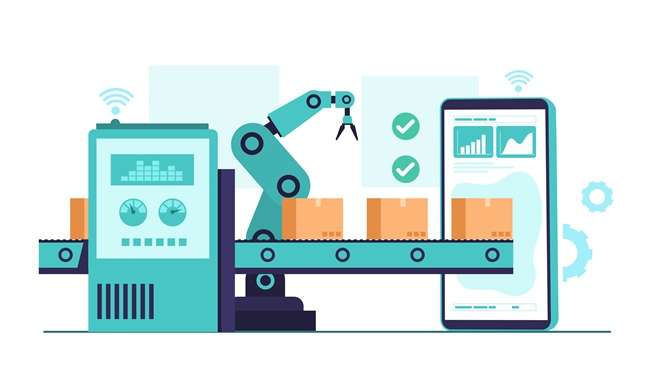
Material Handling Automation Solutions: A Must-read Guide
If you’re thinking why there’s a pressing need for material handling automation solutions across various industries, you’re reading the right blog.
Let’s take a look at some statistics (Courtesy: Vecna Robotics and CITE Research).
- The majority of the material handling automation market is facing labor shortage by 10% to 25%.
- Over 70% supply chain professionals believe that material handling automation is positive for both workers and companies due to benefits such as improved retention rate, upskilling, reduced workload, time saving, etc,.
- E-commerce leads the Autonomous Mobile Robot (AMR) adoption rate at 39% with automotive closely behind at 38%.
These statistics prove that material handling automation is not a luxury but necessity as a large number of businesses look forward to stay competitive while focusing on saving time, money, and resources.
In this extensive blog, we’ll understand what material handling automation is, its features, benefits, and examples.
What is Material Handling Automation?
Material handling automation is a process that involves using software solutions, technological devices, and computerized robots for storage and movement of products from one place to another in your warehouse or manufacturing plant.
While automated material handling solutions implement automated equipment to perform the majority of movement of goods, manual material handling primarily involves deploying human resources to move around materials, which includes lifting, pulling, pushing, etc,.
Next up, we will take a look at some important features of modern-day material handling automation engineering solutions.
Vital Components of Material Handling Automation Systems
Material handling automation systems comprise of various key components that work in tandem to ensure quick and accurate material handling, movement, storage, etc,. Let’s take a look at these components and their functions.
Material Handling Equipment
Material handling equipment covers all machinery that is used to store, move, and control materials by using AGVs, robotic arms, palletizers, conveyor belts, ASRS, etc,.
Control Systems
Control systems such as distributed control systems (DCS) and programmable logic controllers (PLC) coordinate and manage the functioning of material handling automation systems.
Sensors and Actuators
Sensors and actuators play a key role by enabling material handling automation systems to accurately control and monitor different processes to ensure streamlined operations.
Software/User Interfaces
Material handling automation systems usually depend on various software applications to control different processes, like system diagnostics, inventory control, etc,. Similarly, user interfaces are also vital for enabling human operators to manage handling automation systems.
Power and Energy Management
A reliable and consistent power supply is required to ensure seamless operation of material handling automation systems. It involves designing and executing electrical distribution systems, choosing ideal power sources, and putting to practice energy management strategies to minimize energy consumption and costs.
Communication
Good communication and networking hold key for integration of different components of material handling equipment systems to ensure their hassle-free functioning. Wired/wireless communication protocols and/or industrial communication technologies are required for reliable and secure communication flow across the organization.
Types of Automation Services
We have read about important features of material handling automation systems, now we will take a look at different types of automation services offered by companies specializing in automation of material handling equipment. These services can vary from basic upgradation to complete turnkey solutions.
CAD/CAM support
Computer-Aided Design (CAD) and Computer-Aided Manufacturing (CAM) are used to design and create prototypes, final products, and production runs of products.
Equipment design
Equipment designs and their upgrades are meant to improve the machine performance and lower production costs. Palletizers, sorters, and conveyors are some vital equipment in this context.
System design and integration
System design and integration services is the procedure of designing and integrating a complete solution for material handling operations within the storage facility.
Factory automation
Factory automation is a process where entire production operations are automated through the use of hydraulic systems, robotic arms, etc., in manufacturing facilities to build complex solutions.
Turnkey solutions
Turnkey solutions providers are responsible for covering a complete project, from start to finish, which usually involves controls, handling, and equipment.
5 Super Benefits of Material Handling Equipment Automation Systems
Automation of material handling equipment by a large number of companies across various industries has led to a noticeable increase in the overall efficiency and accuracy of material handling and storage.
Here are some key benefits of the automation of material handling equipment system solutions.
Staff safety.
One of the most important benefits of automation in material handling is the enhanced safety of staff present in the warehouse. Since bulk of the lifting and moving is carried out by robots, lifts, pallet trucks, fork trucks, etc, it greatly reduces the chances of human error and potential injuries while saving time otherwise consumed due to manual material handling processes.
Improved quality control.
Use of automated machines for inspections results in improved quality control as more errors are identified and there are lesser chances of rework and waste production.
High in production.
Automated material handling enables facilities with more efficiency and flexibility as they get the capacity to manufacture different materials and quickly make changes in processes. Supply chain and logistics managers can issue commands to automated equipment and process data from a central location.
Easy data access.
Logistics managers, warehouse supervisors, and other company employees can easily access data at any time, on any device. Using the information, different departments within a facility can plan ahead of potential changes and delays.
Skill upgradation.
Automated material handling equipment does not mean replacing human resources by machines and taking up their jobs. Rather, these act as a significant assistance system for the human workforce and relieves much of their workload. With automation, employees are required to acquire new knowledge and develop new skills so as to be proficient in using the latest technology for material handling.
Conclusion
Material handling automation is now considered as an integral component of contemporary industrial processes as it offers benefits in the form of reduced labor costs, improved efficiency, and enhanced safety.
Latest innovations in sensors, AI, machine learning, key components, etc., are making it easier for warehouse managers and employees to streamline and optimize their material handling and management processes. The role of engineers is crucial as they are responsible for understanding and implementing the key components and best practices of this field.
Bursys offers an extensive range of material handling automation solutions that improve efficiency, accuracy, and safety in a wide range of industry verticals. Got questions? Feel free to ask us at contactus@bursys.com